シリコンウエハは半導体チップの原材料です。
現代生活に欠かせない半導体はそのほとんどがシリコンウエハから作られます。
そんなシリコンウエハですが、基になるのはどこにでもある石ころです。
石ころから半導体用のシリコンウエハがどのようにしてできるのかについて誰にでもわかるように解説します。
ぜひとも最後までご覧ください。
【プロフィール】
- 上場企業の現役半導体プロセスエンジニア
(経験10年以上) - 多くの材料メーカーや生産委託先企業との業務経験あり
- 著書を出版しました
- 詳しいプロフィールはこちらからどうぞ
- 半導体に興味関心がある
- 半導体を勉強したい学生さんや社会人の方
動画で解説:シリコンウエハができるまでの工程
半導体ができるまで
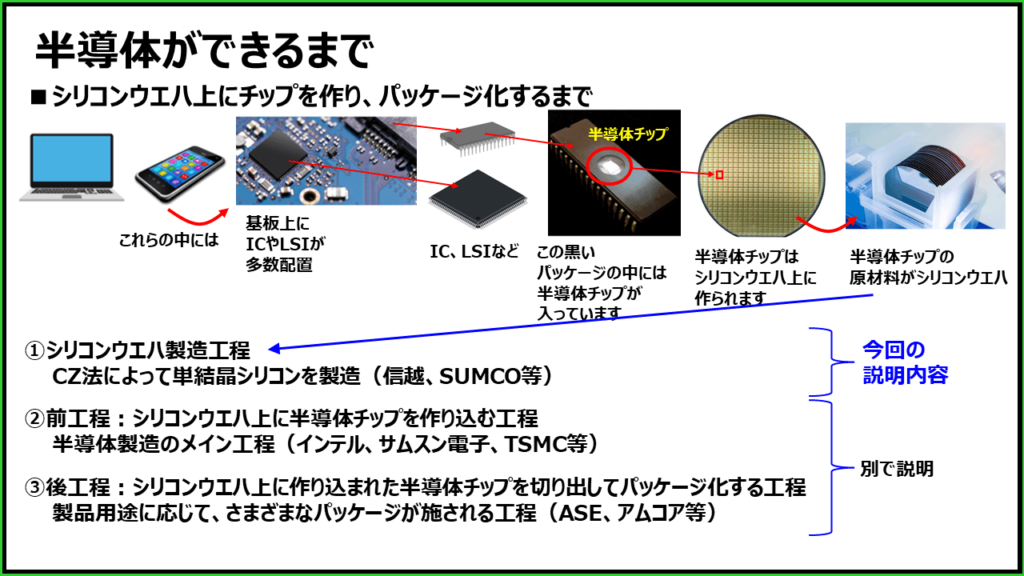
まずは現代生活に欠かすことができない、「半導体」ができるまでを最終製品から逆にみていきましょう。
私たちが普段使っているパソコンやスマホの中には、黒色や緑色をした基板上に電子部品が多数搭載されています。
その中にICやLSIがあり、これらの中に半導体チップが入っています。
半導体チップはシリコンウエハ上に作り込まれます。
そのため、半導体チップの原材料がシリコンウエハということです。
半導体チップができまでの工程を分解しますと、以下の3工程です。
- シリコンウエハができるまで(シリコンウエハ製造工程)
- シリコンウエハ上にチップを作り込むまで(前工程)
- チップを切り出してパッケージ化するまで(後工程)
このうち、この記事ではシリコンウエハができるまでについて解説していきます。
そもそもシリコンウエハとは
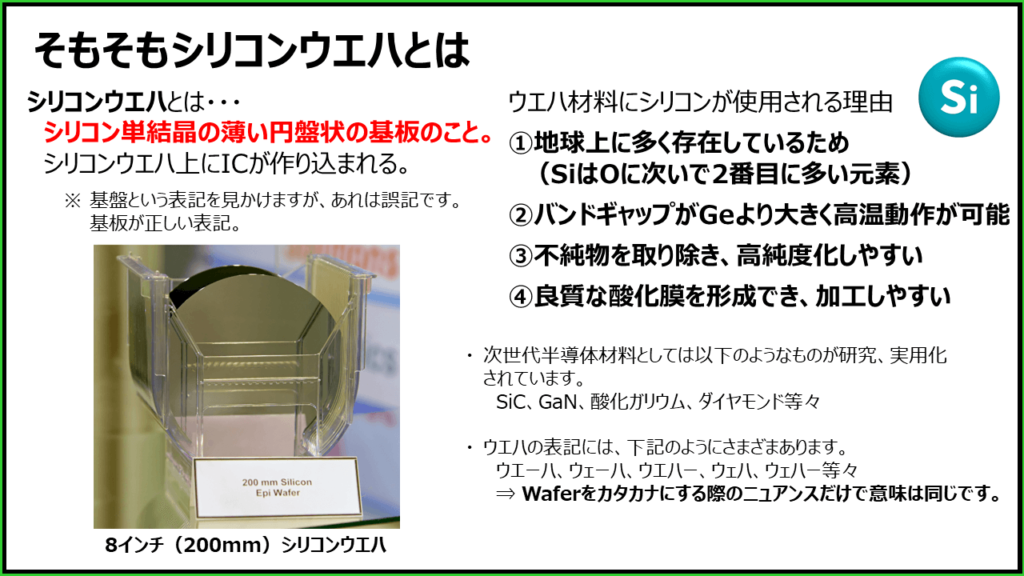
シリコンウエハとは、シリコン単結晶の薄い円盤状の基板のことです。
シリコンウエハ上に半導体チップ(=IC)が作り込まれます。
たまに基盤との表記を見かけますが、あれは誤記で正しくは基板です。
- 地球上に多く存在しているため
- バンドギャップがGeより大きく高温動作が可能
- 不純物を取り除き、高純度化しやすい
- 良質な酸化膜を形成でき、加工がしやすい
ウエハの材料にシリコンが使用されている理由は大きく4つあります。
①地球上に多く存在しているため。
シリコンは元素として地球上に2番目に多く存在します(一番多いのは酸素)。
レアメタルのように存在自体が希少なものではありません。
②バンドギャップがGeより大きく高温動作が可能
半導体黎明期に研究開発されていたGe(ゲルマニウム)は60℃くらいまでしか動作保証ができません。
これは電子物性論で出てきますその材料が持つバンドギャップという特性値に由来します。
シリコンは200℃近い高温動作が可能であるため、車のエンジンルームなど広く使用することができます。
③不純物を取り除き、高純度化しやすい
半導体チップを製造するためには材料を半導体グレードと呼ばれるほどの高純度化が必要です。
後で説明するようにシリコンでは各化学手法を使い高純度化することができます。
④良質な酸化膜を形成でき、加工がしやすい
シリコンは酸素と結合してSiO2という絶縁性が高い酸化膜を形成することができます。
半導体プロセスではこの酸化膜を使うことがひとつのブレイクスルーとなりました。
プレーナ技術と呼ばれるプロセスです。
とは言え、シリコン以外にも次世代半導体材料としては以下のようなものがあります。
- シリコンカーバイト(SiC)
- ガリウムナイトライド(GaN)
- 酸化ガリウム
- ダイヤモンド 等
これらの材料は色々な特性値でシリコンに対する優位性を持った材料です。ただし、SiCとGaNが一部で実用化されている以外は、まだまだこれからです。
ちなみに「ウエハ」の表記にもさまざまなものがあります。
例えばウエーハ、ウェーハ、ウエハー、ウェハ、ウェハーなどをみかけます。
ただし意味はすべて同じです。あくまでも個人的な見解ですが「ウエハ」が一番しっくりきます。
シリコンウエハの大きさ(口径)とは
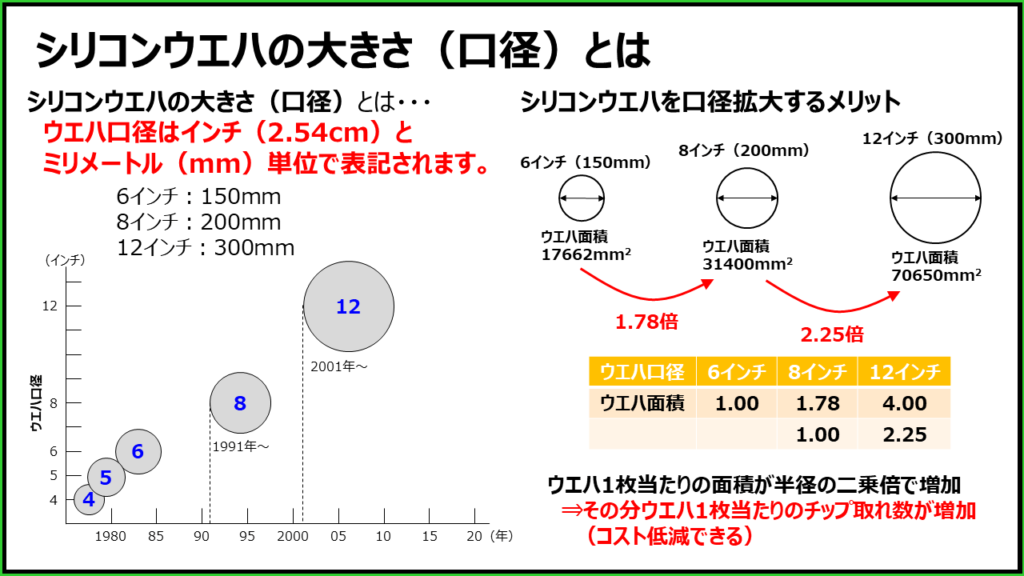
次にシリコンウエハの大きさ(口径)についてみていきましょう。
ニュースなどで300mmウエハの新工場を建設、などの報道を聞くことがあります。
シリコンウエハの大きさはインチとミリメートルで表記されます。
1インチは2.54cmですので、
- 6インチ:150mm
- 8インチ:200mm
- 12インチ:300mm
となります。
現在、世界の主流サイズは12インチ(300mm)ですが、6インチや8インチのシリコンウエハも作られています。
特殊な仕様のウエハであれば近年ではどんどん減っていますが、4インチや5インチも一部で作られています。
ウエハ口径は、技術の進展とともに拡大をしてきました。
1970年代から80年代に4インチ、5インチ、6インチとなり、8インチは1991年から、そして12インチは2001年から量産に使用されています。
ウエハ口径を拡大するメリットは単純で、ウエハ面積が増えることで同じチップサイズであればウエハ1枚当たりの取れ数が増加する(=コストが低減できる)とこです。
ウエハ面積は半径の二乗倍で増加しますので、6インチのウエハ面積を1.00としたとき、8インチは1.78となり、12インチでは4.00になります。
シリコンウエハ生産量と市場シェア
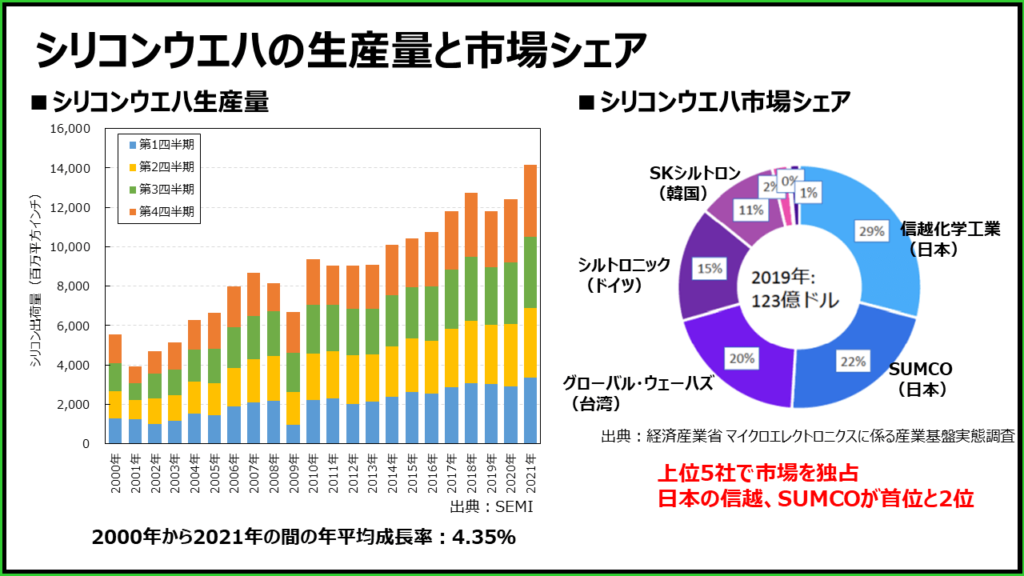
シリコンウエハの生産量と市場シェアについても確認してみましょう。
シリコンウエハの生産量は上図の通り多少の凸凹はありますが、年々増加していることが分かります。
半導体市場全体が拡大していますので、それに伴いシリコンウエハの生産量が増加している訳です。
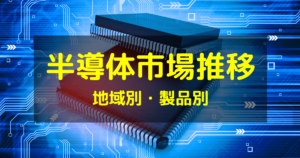
シリコンウエハ市場は日本の信越化学とSUMCOが首位と2位になっており、この2社で過半のシェアを占めています。
信越化学とSUMCOに台湾のグローバルウェーハズ、ドイツのシルトロニック、韓国のSKシルトロンが続き、この5社で市場の9割以上を占めています。
シリコンウエハができるまで
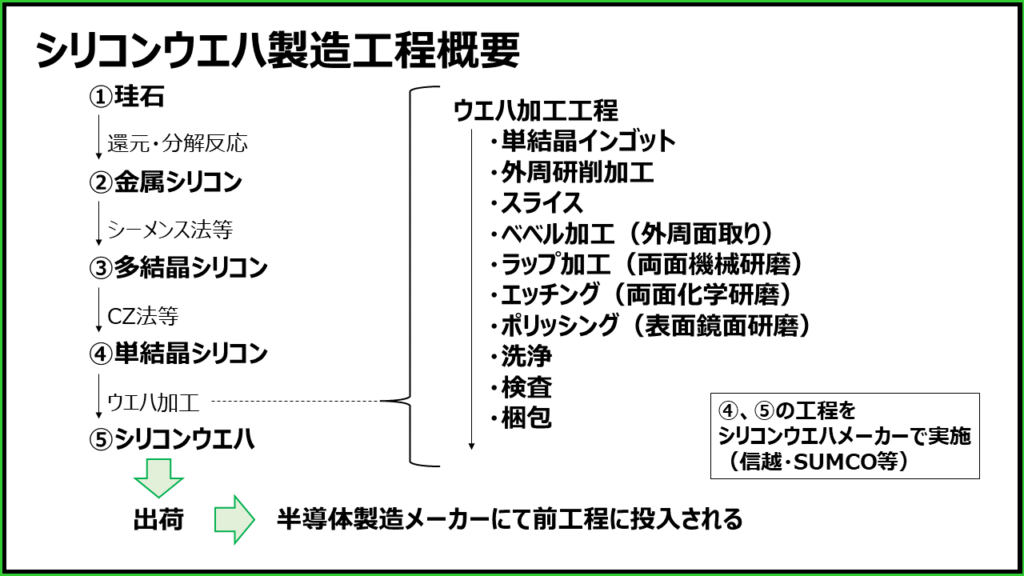
ここからシリコンウエハができまでの製造工程をみていきましょう。
シリコンウエハができるまでの工程は大きく5つに分けられます。
- 珪石採取
- 珪石を還元分解反応から金属シリコンを製造
- 金属シリコンをシーメンス法等によって多結晶シリコンを製造
- 多結晶シリコンからCZ法等によって単結晶シリコンインゴットを製造
- 単結晶シリコンインゴットをスライスして加工、シリコンウエハが完成して出荷
これらの工程のうち、信越化学とSUMCOなどのシリコンウエハメーカーでは④、⑤の工程を行っています。
製造工程① 珪石
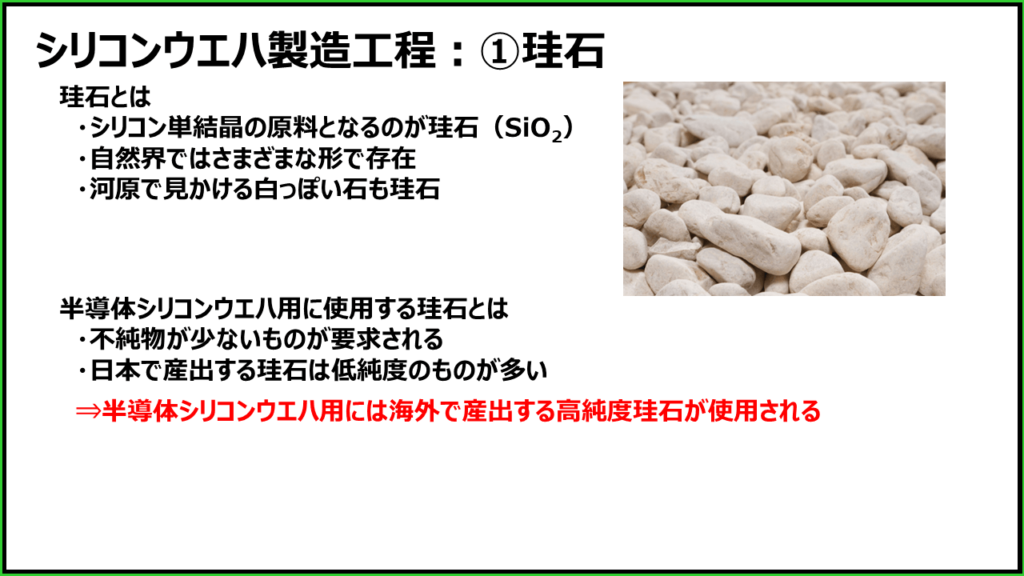
シリコンウエハの原材料となるのが珪石です。
既述の通り、シリコンは地球上で二番目に多く存在している元素であり、珪石は自然界にはさまざまな形で存在しています。
河原で見かける白っぽい石も珪石です。
つまり、シリコンウエハはその辺りに転がっている石ころからできていると言うことができます。
ただし、シリコンウエハに使用する珪石は不純物が少ないものが要求されます。
日本で産出する珪石は低純度のものが多く適していません。
そのためシリコンウエハ用には海外で産出する高純度珪石が使用されます。
高純度珪石はノルウェーやブラジルなどの鉱山から採取されます。
製造工程② 金属シリコン
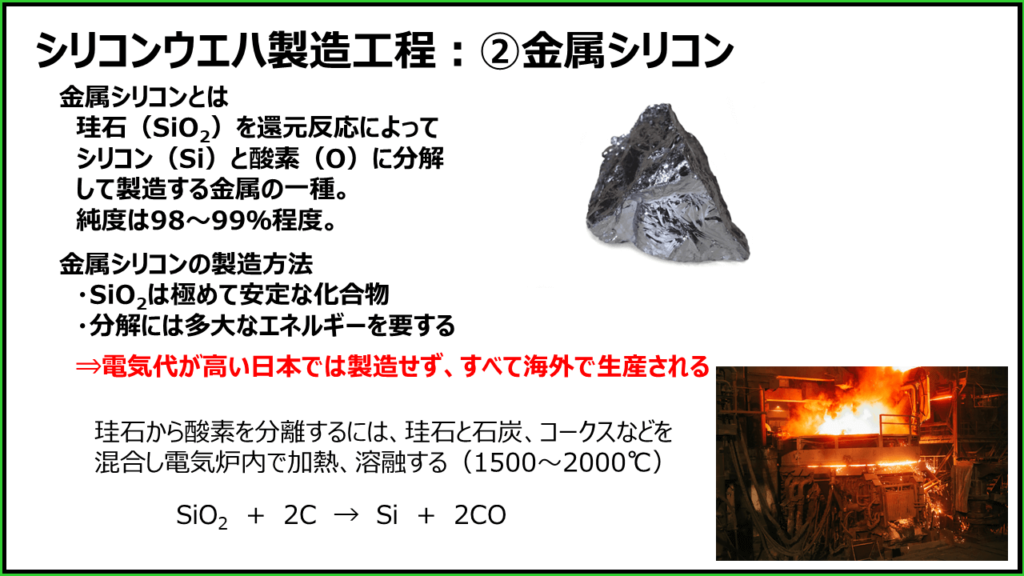
珪石はシリコンと酸素の化合物であり、それ以外にもさまざまな不純物を含んでいます。
まずは珪石を還元反応によってシリコンと酸素に分解します。
そうすることでできる金属の一種が金属シリコンです。
金属の特徴である光沢を見ることができます。
金属シリコンの純度は約98から99%程度になります。
金属シリコンの製造方法は、珪石と石炭、コークスなどを混合して電気炉内で加熱、溶融することです。
SiO2は化学的に極めて安定な物質で、シリコンと酸素に分解するためには多大なエネルギーを要します。
つまり電気代がとてもかかるということです。
そのため、電気代が高い日本では採算性が合わないため製造せず、すべて海外で生産されています。
金属シリコンは全量を輸入に頼っています。
製造工程③ 多結晶シリコン
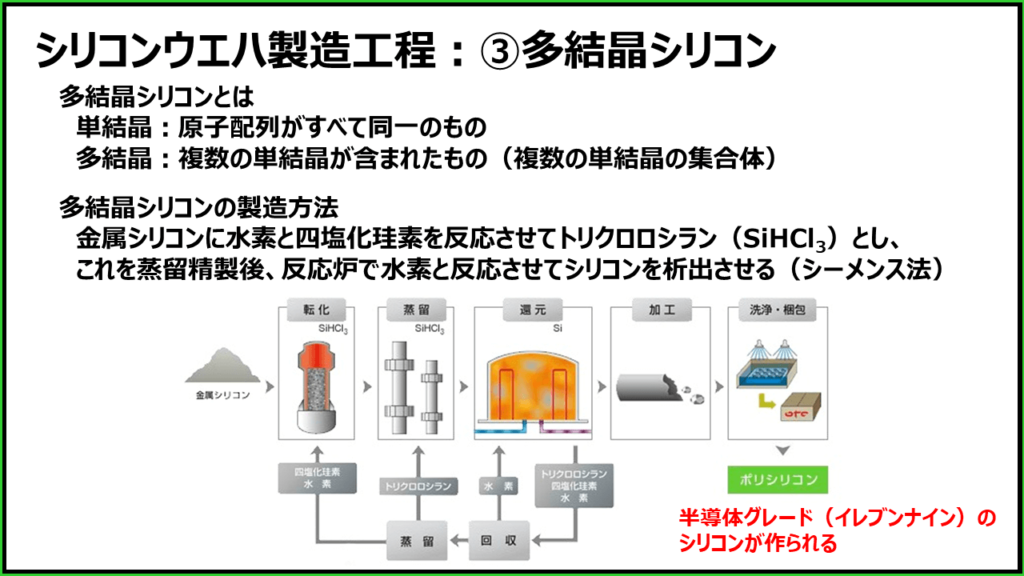
金属シリコンを材料にして多結晶シリコンを製造します。
多結晶シリコンの多結晶とは複数の単結晶(原子配列がすべて同一のもの)が含まれたもののことです。
多結晶シリコンの製造方法はシーメンス法があります。
これはその名の通り、ドイツのシーメンス社で開発された手法です。
金属シリコンに水素と四塩化珪素を反応させてトリクロロシランとし、トリクロロシランを蒸留精製して純度を極限まで高めた後に、反応炉で水素と反応させてシリコンを析出されるというものです。
このあたりの詳細は化学的な知識がないと難しいところです。
簡単に言いますと、金属シリコンをガス化して沸点の異なる成分を分離することで不純物を取り除き、高純度化した後に元のシリコンに戻すということです。
これによって半導体グレードと呼ばれるイレブンナインまたはトゥエルブナインの高純度シリコンが完成します。
製造工程④ 単結晶シリコン
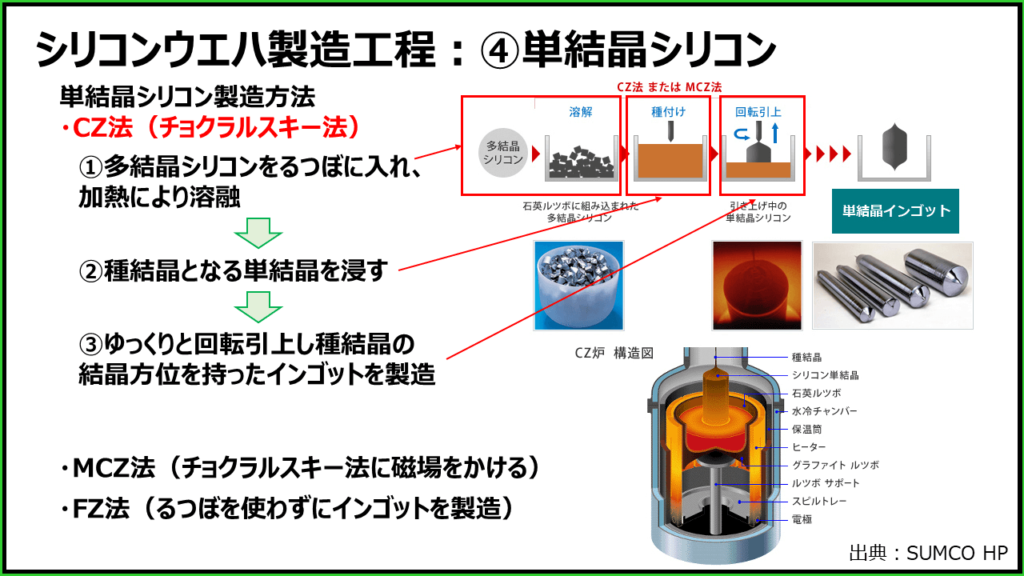
多結晶シリコンを材料にして単結晶シリコンのインゴットを製造します。
単結晶シリコンインゴットはCZ法(チョクラルスキー法)で製造されます。
- 多結晶シリコンをるつぼに入れ、抵抗加熱か高周波加熱によってシリコンを溶融
- 種結晶となる単結晶を溶融したシリコンに静かに浸す
- ゆっくりと回転しながら種結晶を引き上げる
- 単結晶シリコンインゴットが完成
単結晶シリコンインゴットの製造にはCZ法以外に、CZ法に磁場をかけるMCZ法や、るつぼを使わずに製造することで低酸素濃度のインゴットを製造するFZ法などがあります。
製造工程⑤ ウエハ加工
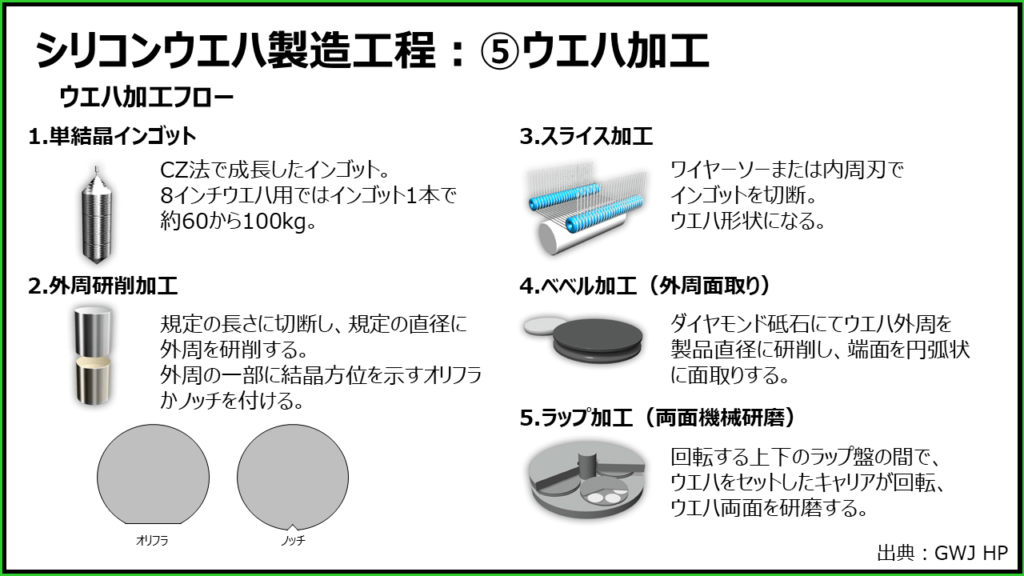
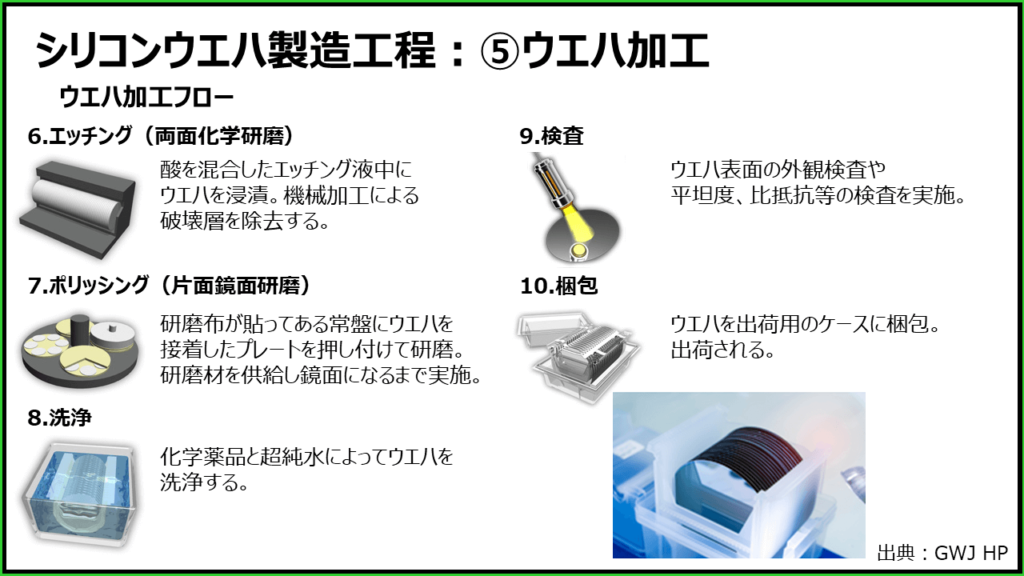
最後に単結晶シリコンインゴットを加工してシリコンウエハ製造します。
8インチ用インゴットは重量が約60から100kgあります。
12インチ用では100kg以上あります。
インゴットを規定の長さに切断します。
そして規定の直径に外周を研削します。
外周の一部には結晶方位を示すオリフラ(オリエンテーションフラット)かノッチを入れます。
インゴットをワイヤーソーか内周刃によって切断します。
ここでウエハ形状となります。
外周部を研削し、ウエハ端面を円弧上に面取りします。
ウエハ端面は一般的に上下対象面取りですが、製品仕様によっては非対称面取りの場合もあります。
ウエハ表裏面を機械的な研磨をして平坦にします。
ウエハ表裏面を化学的に削ります。
機械加工によってウエハ表裏面部には破壊層ができていますので、破壊層を除去します。
ウエハ表面を鏡面研磨します。
鏡のようにピカピカになります。
ウエハ表裏面を化学薬品と超純水で洗います。
ウエハ表面の異物検査や、平坦度、比抵抗などの各種検査項目を検査します。
シリコンウエハが完成!
検査に合格したウエハを梱包し、出荷します。
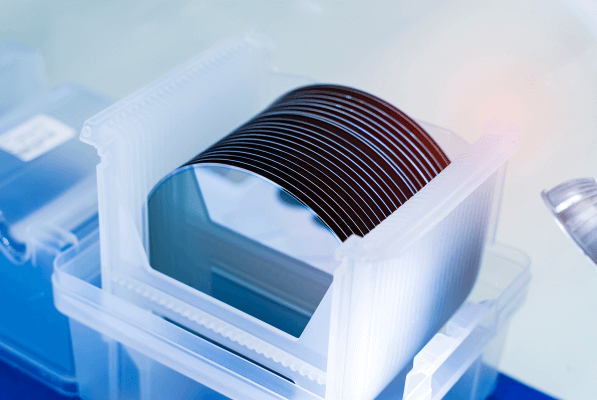